Risolvere problemi di perdite sulle portiere delle automobili
Scanning and Inspection Pty si rivolge a PolyWorks® e analizza il rapporto tra il telaio della portiera e la carrozzeria dell'auto in meno di 1 ora.
I produttori sanno quando qualcosa va storto e scoprire il perché è spesso un processo molto più complesso. Le successive ricerche richiedono tempo, denaro e altre risorse. Anche una volta che il problema è stato finalmente identificato, effettuare adeguamenti quantificati è un altro passaggio della soluzione del problema. A volte il pezzo prodotto è diverso da quello progettato, o diverso da come dovrebbe essere o è stato in passato, ma di quanto, dove e in quale direzione? Per un importante produttore di automobili australiano, identificare la causa delle perdite sulle portiere era una priorità.
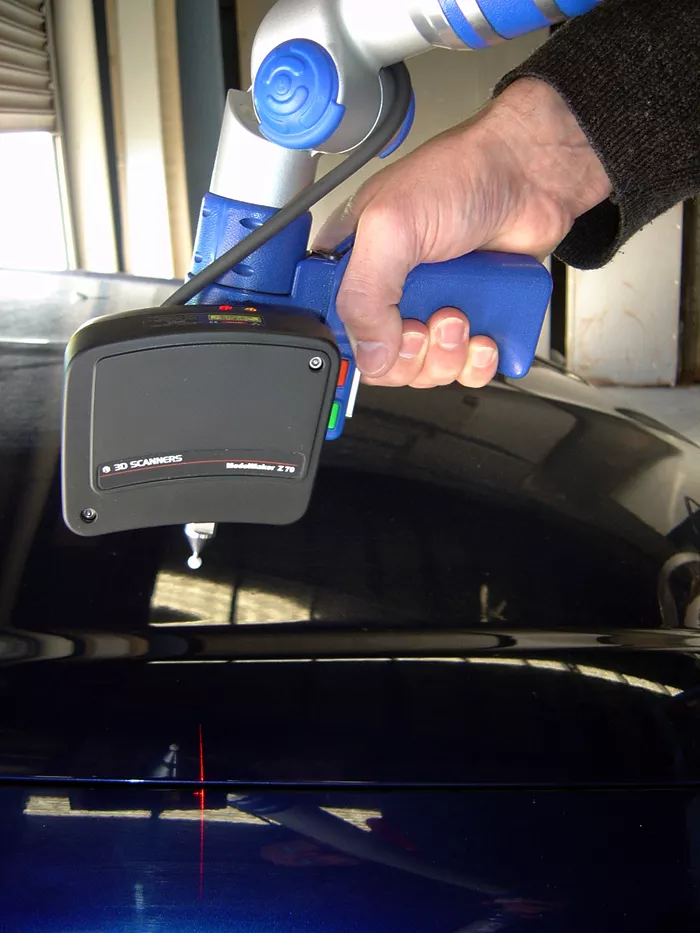
ModelMaker Z70 montato su un FaroArm
La sfida
Un produttore di automobili ha recentemente sperimentato uno di questi scenari di produzione inevitabili. Hanno riscontrato variazioni nell'allineamento di alcune guarnizioni delle porte passeggeri dell'abitacolo che hanno prodotto e assemblato. Era evidente che alcune automobili che erano state prodotte durante uno specifico momento della produzione automobilistica erano come ci si aspettava, le portiere e le guarnizioni erano tutte allineate con il resto della carrozzeria senza soluzione di continuità. Tuttavia, quelle uscite dalla linea di produzione in una fase successiva hanno subito presentato perdite d'acqua durante i test. Il primo compito è stato individuare il punto di passaggio dell'acqua, ma l'analisi che ha richiesto più impegno è stata quella relativa al rapporto tra il telaio della portiera e la carrozzeria dell'auto. Ma capire cosa c'era di diverso rispetto ai veicoli che non perdevano, e determinare quanto, dove e in quale direzione ha creato una serie di difficoltà.
Se un lotto è uscito dalla produzione e non ha presentato problemi di perdite, mentre altri prodotti in una fase successiva hanno avuto perdite, devono essere in qualche modo diversi nella loro struttura. In che cosa si differenzia il telaio problematico da uno che invece non lo è? Per capire quali modifiche devono essere apportate durante la produzione, il cliente deve essere in grado di quantificare la discrepanza. È necessario valutare il rapporto e le variazioni tra i telai "buoni" e quelli "cattivi". È stata acquisita un'analisi comparativa dettagliata e, grazie alla più recente tecnologia di scansione laser e alla suite di programmi PolyWorks®, è stato possibile riuscirci in poche ore.
La soluzione
Acquisizione di dati
Per acquisire in modo rapido ed efficiente le informazioni sulla superficie, gli specialisti di Scanning and Inspection hanno utilizzato uno scanner laser montato su un braccio articolato. Il tipo di scanner laser utilizzato per questa applicazione è stato il ModelMaker Z70, uno scanner di alta qualità in grado di digitalizzare una superficie ad una notevole densità pari a 0,05 mm x 0,05 mm, circa 400 punti per millimetro quadrato. Il risultato è una rappresentazione digitale realistica, completa e tridimensionale del pezzo, una moltitudine di dati che aspettano solo di essere trasformati in informazioni utili. Lo scanner ottiene il suo riferimento 3D da una CMM portatile, in questo caso un Platinum FaroArm, che misura una ripetibilità che va da ±0,0051 mm a seconda delle dimensioni. Il FaroArm e il Laser Scanner MMZ70 sono stati portati in posizione sul posto grazie a un treppiede per impieghi gravosi, con cui l'hardware ha potuto essere comodamente posizionato accanto alle portiere dell'auto in questione. L'acquisizione dei dati di superficie ha richiesto solo pochi minuti per ogni auto.
Il processo PolyWorks
Una volta raccolti i dati di scansione, è iniziata la fase di post-elaborazione dell'analisi. Grazie alle funzionalità di PolyWorks, gli specialisti di Scanning and Inspection Pty Ltd. hanno virtualmente allineato i dati scansionati con il laser dalla macchina "che perde" a quella "buona", e hanno eseguito analisi avanzate di misura e di confronto. Tuttavia, prima di eseguire le analisi comparative, è stato necessario condurre una serie di manipolazioni delle nuvole di punti in PolyWorks.
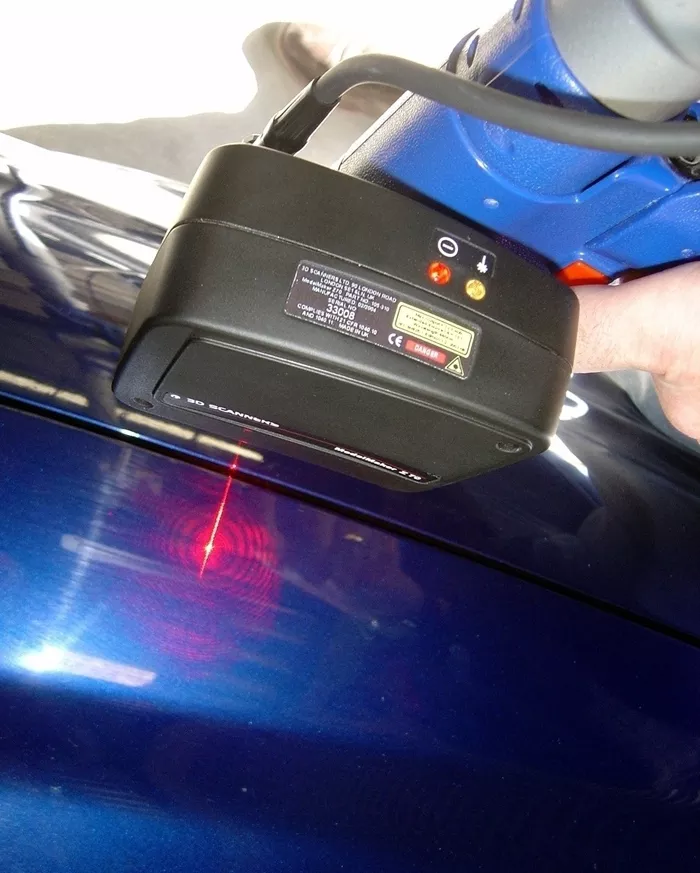
Acquisizione di dati
Affinamento dell'allineamento delle scansioni
Durante la fase di acquisizione dei dati del lavoro, sono stati ottenuti diversi passaggi di scansione. Ogni patch di scansione viene allineata automaticamente utilizzando la tecnologia di allineamento nativa del braccio articolato che fornisce il riferimento spaziale per il cambio di posizione dello scanner laser. La maggior parte delle nuvole di punti acquisite dallo scanner laser "si siedono" sopra ad altre che sono già state calcolate da altri passaggi dello scanner. Alcune parti del pezzo vengono quindi misurate più di una volta. Queste aree di dati a più livelli vengono definite aree di sovrapposizione.
Per affinare la nuvola di punti allineata ottenuta dalla CMM portatile, il modulo PolyWorks IMAlign utilizza queste aree di sovrapposizione per riallineare tutte le scansioni. In primo luogo, è stata eseguita un'analisi delle deviazioni sulla nuvola di punti allineata. PolyWorks calcola automaticamente le distanze medie tra ogni scansione sovrapposta e mostra un colore che rappresenta un valore di deviazione. Gli utenti possono individuare subito le scansioni fuori tolleranza e che possono essere migliorate attraverso il riallineamento.
Infine, usando la tecnologia di allineamento "best-fit" di PolyWorks, è stato eseguito un riallineamento. Per evitare di "scivolare" tra le patch nella stessa area, vengono automaticamente impostati otto punti di controllo per ciascuna scansione, che limitano i gradi di libertà. Questa caratteristica differenzia PolyWorks dalle altre soluzioni di allineamento delle scansioni, che spesso presentano problemi di scorrimento durante il processo di allineamento. Una volta eseguito l'allineamento best-fit vincolato, viene calcolata una nuova analisi delle deviazioni e viene visualizzata una mappa di colori.
L'ultimo passaggio consiste nel creare un modello di nuvola di punti a un solo strato, calcolando in modo intelligente la media di tutte le scansioni sovrapposte usando la tecnologia PolyWorks di "riduzione delle sovrapposizioni". La nuvola di punti ottenuta può ora essere trasformata in una superficie che verrà utilizzata per ulteriori analisi, ad esempio per i confronti tra gli sportelli. La metodologia di scansione è stata la stessa sia per le auto "che perdono" che per quelle "buone". Tutte le rifiniture periferiche sono state rimosse dai telai dei finestrini e degli sportelli in modo tale da mettere in evidenza solo i componenti in acciaio strutturale post-produzione. Gli sportelli sono stati chiusi durante tutto il processo di acquisizione dei dati e le relative aree associate alle perdite sono state scansionate con il laser MMZ70.
Mentre la striscia laser viene spostata sulla superficie, raccogliendo decine di migliaia di punti 3D al secondo, la superficie successiva viene immediatamente visualizzata sullo schermo del computer. Le capacità di questa visualizzazione in tempo reale della superficie delle nuvole di punti hanno permesso di individuare le aree che non erano state rilevate o che dovevano ancora essere scansionate al momento della misurazione e, di conseguenza, di tenerne conto.

Creazione di un modello poligonale
Creazione di un modello poligonale
Per poter confrontare le superfici dei telai delle portiere "buone" e "cattive", Scanning and Inspection ha dovuto convertire le nuvole di punti in qualcosa che potesse essere utilizzato come superficie. PolyWorks ha convertito in un batter d'occhio le decine di milioni di punti della nuvola di punti in una mesh triangolare. Il software ha utilizzato ciascuno dei punti come nodi per i milioni di minuscoli triangoli che ha costruito.
Per descrivere accuratamente le varie forme dell'oggetto scansionato, PolyWorks usa meno triangoli per le sezioni più consistenti della superficie dell'auto e più triangoli quando il contorno diventa complesso, il tutto basato su valori di tolleranza specificati dall'utente. Prima della conversione sono stati definiti anche i parametri relativi alla vicinanza e alla distanza di ricerca, per creare la superficie triangolare e ridurre al massimo il rumore intrinseco del dispositivo di acquisizione.
Confronto degli sportelli
Usando una complessa serie di matematica di "minimi quadrati" e di analisi delle superfici, i due nuovi set di dati della scansione laser triangolati e ottimizzati sono stati posti uno sopra l'altro e allineati usando la tecnologia di allineamento best-fit di PolyWorks. PolyWorks ha quindi sviluppato un modello di distribuzione a colori per evidenziare il confronto tra i due assiemi. La mappa degli errori a colori ottenuta permette di distinguere facilmente i modelli che identificano in che modo lo sportello dell'auto "cattivo" che presenta le perdite si rapporta allo sportello "buono".
Il montante B e le sezioni inferiori degli sportelli presentano un colore verde chiaro (quasi verde acqua) che indica una deviazione inferiore a ±0,5 mm tra i due gruppi di sportelli. Altre zone, come il telaio del finestrino in acciaio saldato allo sportello stesso, sono evidenziate in verde, il che equivale ad una deviazione di ±1-2 mm. Infine, la sezione arancione, situata sul telaio della vettura, indica anche una deviazione di ±1-2 mm.
In altre parole, quando i montanti B delle due vetture erano allineati entro 0,5 mm, i telai dei finestrini della vettura che perdeva erano in realtà posizionati tra 0,5 mm e 2 mm al di sotto di quello del veicolo che non perdeva, uno spazio sicuramente sufficiente per il passaggio dell'acqua.
Vantaggi
I tecnici di Scanning and Inspection hanno effettivamente scoperto che sarebbe stato molto più facile cambiare le saldature responsabili della posizione del telaio dello sportello anziché regolare il telaio. La saldatura in cui il telaio del finestrino coincide con lo sportello è stata regolata in modo tale che il telaio non fosse così basso (rispetto allo sportello che non perdeva).
L'intero processo di ispezione con PolyWorks è stato eseguito in meno di 1 ora.
Le conclusioni tratte dall'indagine vertevano principalmente sulle preoccupazioni del cliente relative al telaio del finestrino del veicolo, o più specificamente sul modo in cui esso veniva saldato al gruppo dello sportello principale. Sono state effettuate le opportune regolazioni in relazione ai trattamenti della saldatura, per fare in modo che il telaio del finestrino non si trovasse più troppo all'interno della sua posizione ideale, come descritto nel progetto CAD iniziale.
La precisione e la flessibilità del FaroArm e dello scanner laser MMZ70, utilizzati in combinazione con lo straordinario software PolyWorks, hanno permesso a questo produttore di automobili di:
- Individuare rapidamente l'origine della perdita
- Misurare con precisione la deviazione fisica degli sportelli "cattivi" rispetto a quelli "buoni" (quanto, dove e in quale direzione)
- Modificare il processo di assemblaggio regolando la saldatura nel punto in cui il telaio del finestrino coincide con lo sportello
- Eseguire l'intero processo di ispezione in meno di 1 ora