Amor pelo design e paixão pela perfeição
A Bushwacker Inc. utiliza os recursos de engenharia reversa do PolyWorks|Modeler™ para ir do conceito ao protótipo em poucos dias.
Por quase 40 anos, a Bushwacker Inc., uma empresa de uma família em Portland, Oregon, vem fabricando pára-lamas e acessórios para pick-ups e utilitários para o mercado secundário de peças automotivas com paixão e orgulho. Reconhecida como uma fabricante líder, a Bushwacker cria designs inovadores e fabrica produtos de alta qualidade. Sterling Logan, engenheiro de design da Bushwacker, afirmou: “Para fazer isso, precisamos de ferramentas de ponta.”
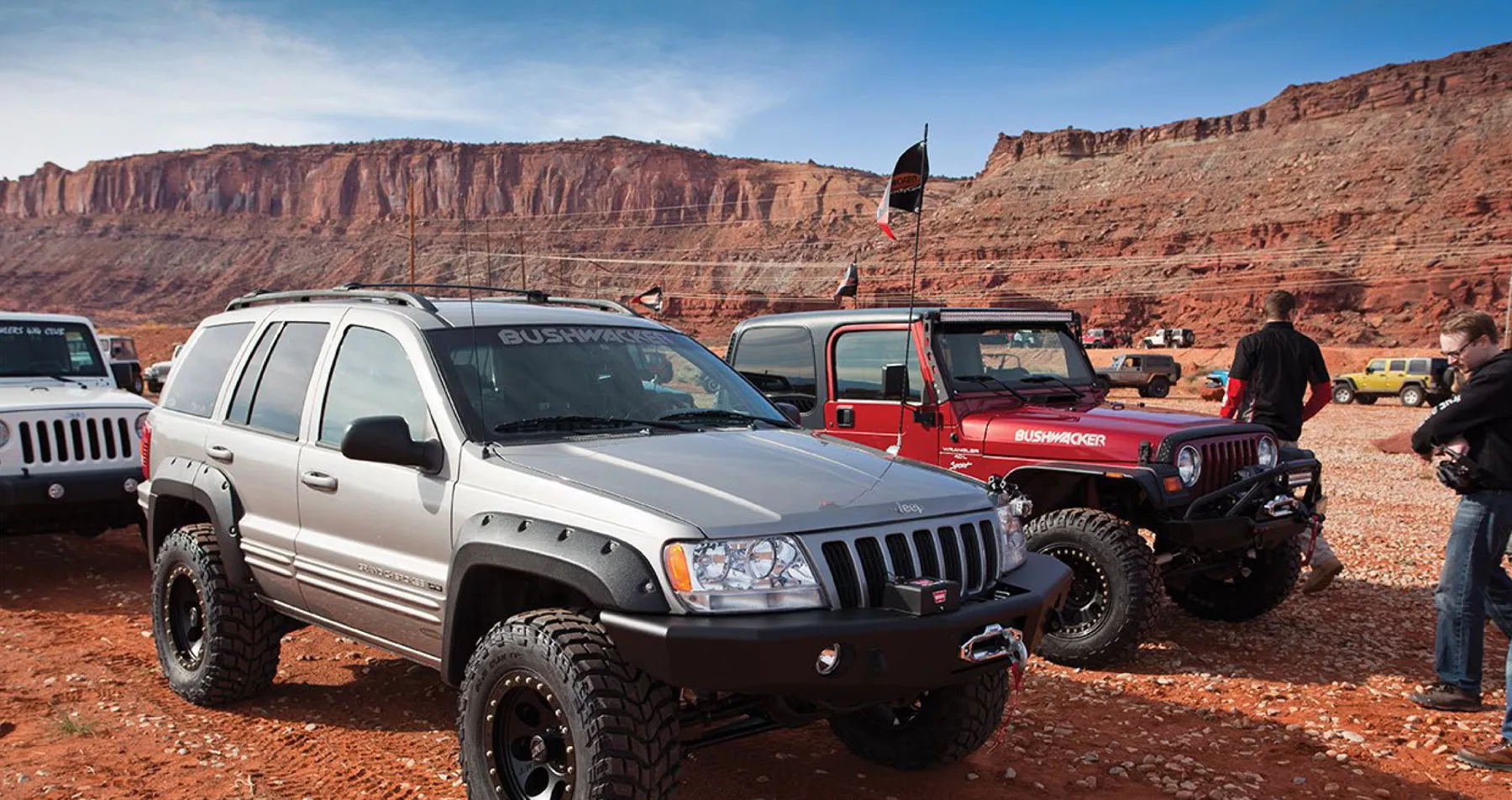
O desafio
A Bushwacker está comprometida com o estilo e a inovação pois são parte integral de cada produto que fabricam. Eles examinam meticulosamente cada detalhe de cada projeto, usando os mais recentes padrões de projeto e fabricação. Para a Bushwacker, a qualidade pode ser resumida em três palavras: ajuste, acabamento e estilo. No entanto, “a qualidade é um alvo móvel”, observou Logan. Os OEMs continuam a elevar o padrão de qualidade do veículo em termos de ajuste e acabamento, enquanto as linhas de estilo da carroceria se tornam cada vez mais sofisticadas. E para permanecerem competitivos, os produtos da Bushwacker devem seguir a mesma filosofia.
Garantindo qualidade para continuar competitiva
“Nossos clientes esperam que os acessórios combinem com as linhas de estilo do veículo. E com as superfícies de alta qualidade que os fabricantes de automóveis produzem, a menor falha ou interferência nas linhas de estilo do veículo torna-se imediatamente óbvia. Portanto, temos que entregar um produto com um encaixe perfeito”, disse Logan. Para atingir esse objetivo, a digitalização 3D é absolutamente essencial.
Depois de fazer experiências com soluções alternativas e serviços de digitalização, a Bushwacker adquiriu um sistema de digitalização de ponta que inclui um braço Romer Infinite 2.0 com sete eixos, um scanner a laser Perceptron ScanWorks V5 e o software de metrologia 3D PolyWorks® da InnovMetric. Conhecer os dados digitais precisos das superfícies de um veículo permite que a Bushwacker concentre seus talentos no projeto de produtos com a confiança absoluta de que o encaixe será perfeito. Com a digitalização 3D, o ajuste é retirado da equação, simplificando o processo e reduzindo as horas de trabalho.
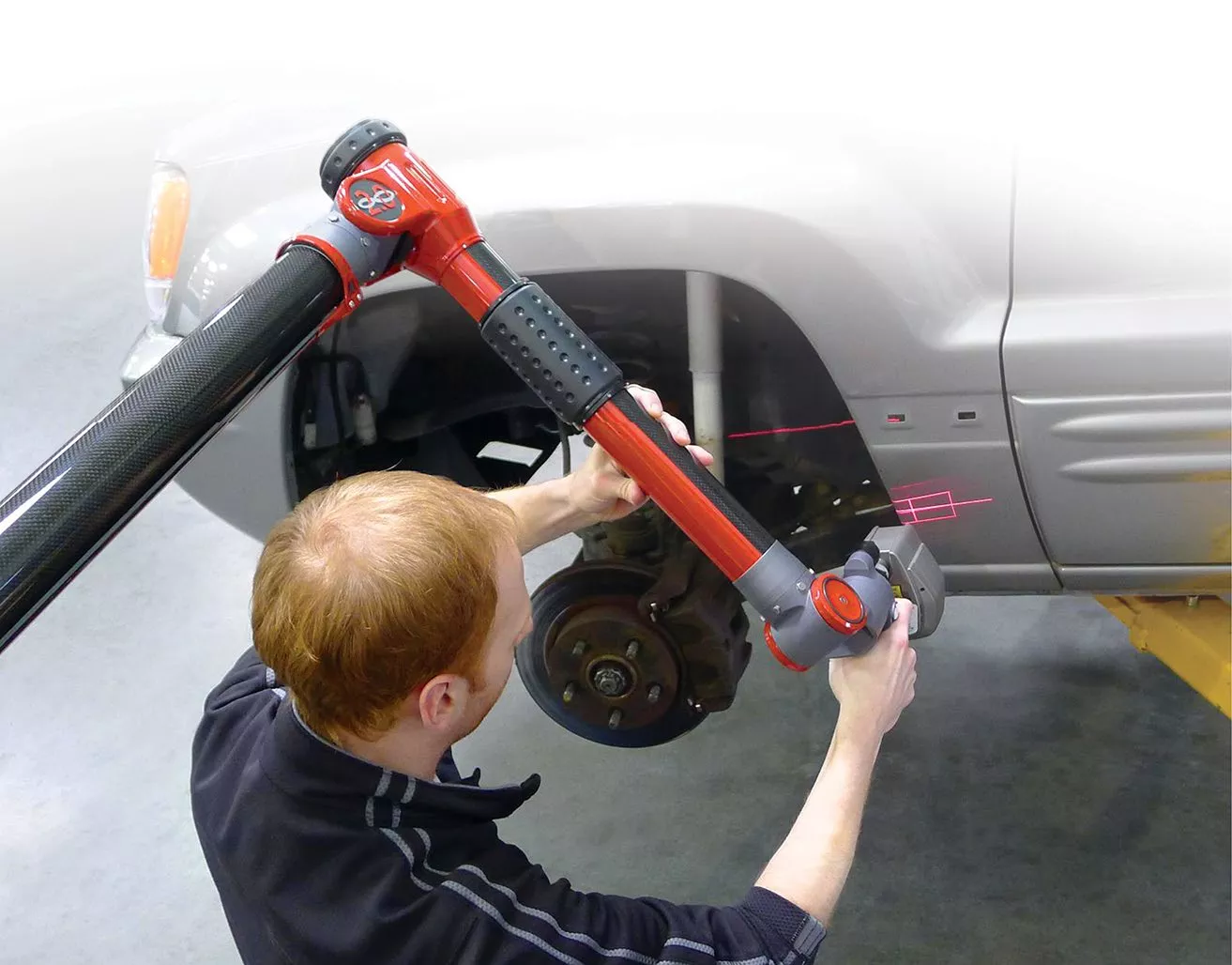
Digitalizando um Jeep Grand Cherokee com um scanner a laser para capturar o painel dianteiro com linhas de estilo e locais de montagem.
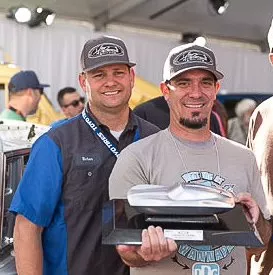
"Com o scanner e o software PolyWorks, podemos ir do conceito ao protótipo em muito poucos dias".
Sterling Logan, engenheiro de projetos, Bushwacker
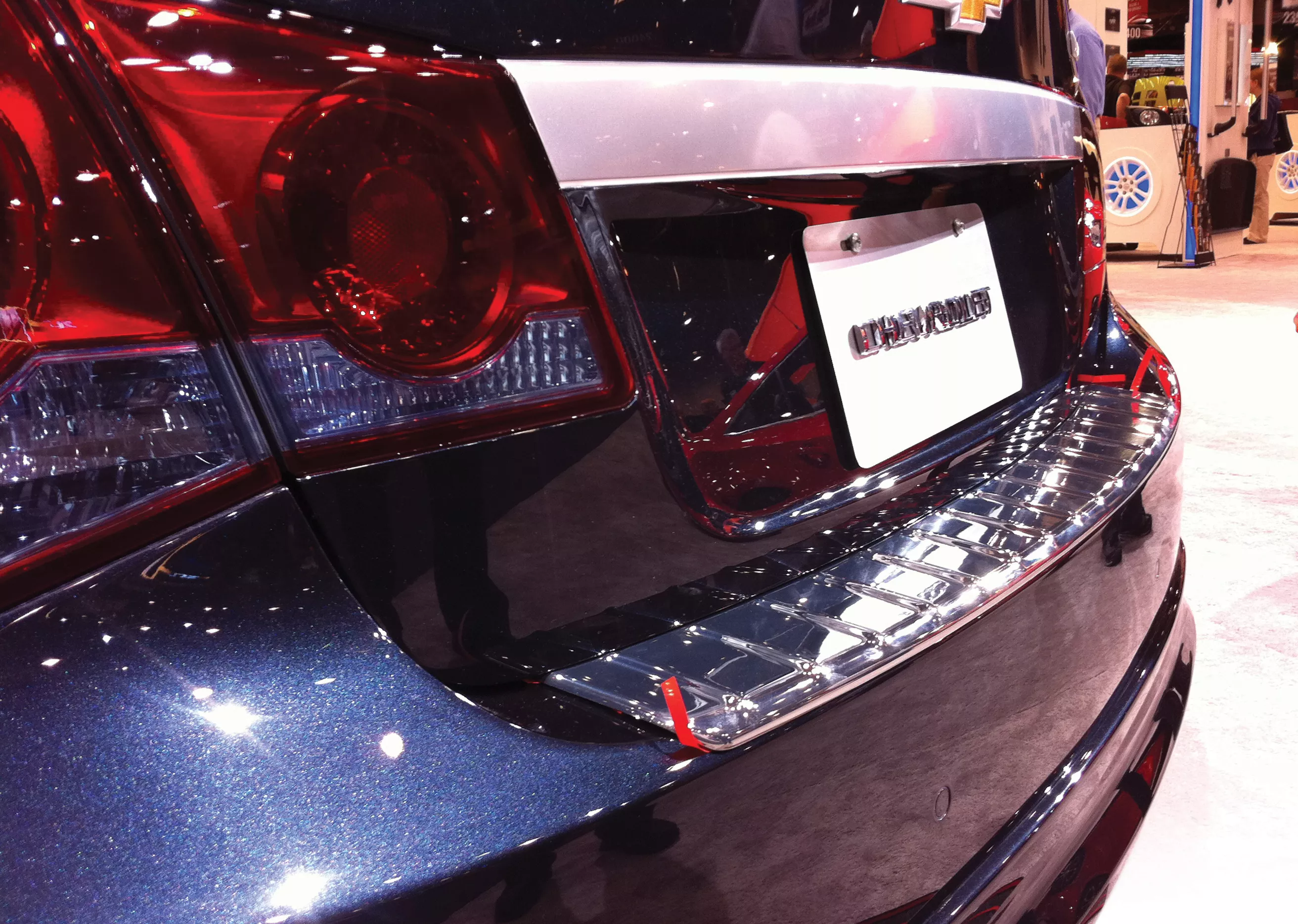
Protetor de pára-choque do Chevrolet Cruze na SEMA, em três dias, do conceito ao design.
Para destacar o rápido tempo de resposta graças à digitalização 3D, Logan citou o seguinte exemplo. “Um cliente entrou em contato conosco alguns dias antes do evento da Speciality Equipment Market Association (SEMA) com um pedido personalizado para projetar um protetor de pára-choque para o Chevrolet Cruze. Em apenas três dias, tínhamos os protótipos dos protetores de pára-choques e chegamos ao show com um produto totalmente novo.”
Logan ilustrou como o produto foi concluído em apenas três dias. No primeiro dia, a Bushwacker digitalizou o Chevrolet Cruze, processou os dados usando o PolyWorks|Modeler e os importou no Siemens NX. No segundo dia, projetaram o protetor do pára-choque e usinaram um molde do protótipo. No terceiro dia, as peças foram fabricadas e enviadas para a feira SEMA por via aérea.
Em seus primeiros anos, a Bushwacker usava o material preferido em oficinas OEM de personalização: argila. Os designers aplicaram argila ao veículo e a esculpiram meticulosamente até atingirem o design desejado. A forma resultante era transferida para modelos de madeira para que o estilo pudesse ser transferido em argila para o outro lado do veículo. Depois disso, eram feitos moldes em gesso a partir dos modelos de argila e os moldes eram usados para fabricar protótipos com ferramentas de termoformação.
De acordo com Logan, esse processo levava muitas horas de trabalho árduo. E, mesmo assim, ainda levaria vários meses até que um molde estivesse pronto para a produção. Logan disse: “Chegávamos perto, mas raramente atingíamos perfeição na primeira tentativa.” Obcecado com a qualidade de seus projetos, a Bushwacker configurou o ajuste e design usando quatro ou cinco ciclos de moldes de protótipo, verificação do encaixe, avaliação visual, modificação de molde, seguida de nova verificação.
“Mas agora, com os recursos de engenharia reversa da digitalização a laser e do software PolyWorks, raramente precisamos fazer alguma alteração em nossos moldes ou projetos de peças. As alterações que fazemos são dedicadas aos ajustes sutis ao design que dão estilo aos nossos para-lamas - cada um projetado para que tenha uma aparência específica”, disse Logan.
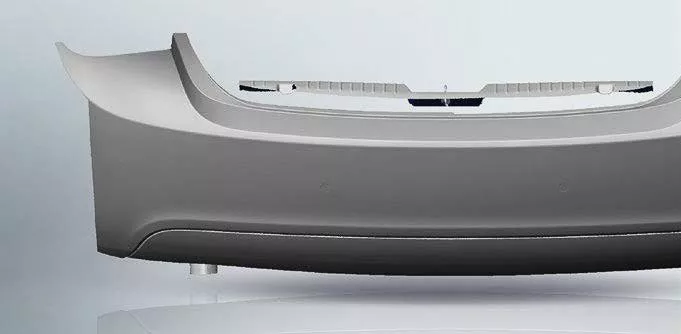
Dados da digitalização do pára-choque traseiro do Chevrolet Cruze e da trava do porta-malas prontos para uso no projeto de criação de uma proteção traseira do pára-choque.
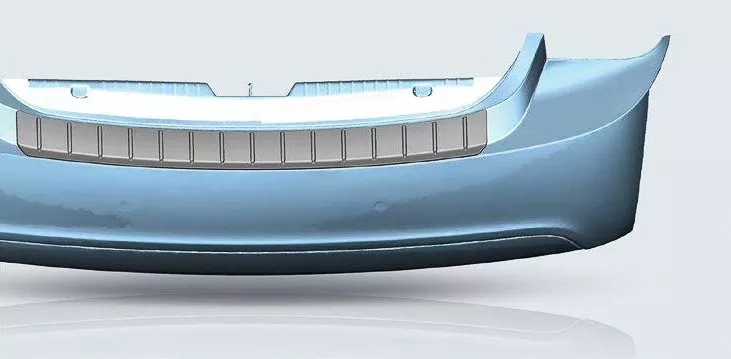
Imagem do CAD mostrando o design final do protetor de pára-choque (em cinza) e sua colocação no Chevrolet Cruz.
Jeep JK: amor pelo design
Logan refletiu sobre o passado versus o presente: “Quando começamos nossa empresa, nossos primeiros alargadores de para-lamas foram para o antigo Jeep CJ. O processo de argila e gesso funcionou bem na época porque a chapa metálica dos para-lamas era plana. Isso definitivamente não é mais verdade para o estilo do corpo do novo Jeep JK.”
O Jeep JK foi um desafio por causa de suas linhas de estilo da carroceria e configuração de montagem. Mesmo com a digitalização 3D, a Bushwacker passou seis meses desenvolvendo seus alargadores de para-lamas patenteados no estilo pocket, alargadores no estilo plano e o estribo protetor lateral Trail Armor. Logan observou que, para todos os outros projetos, a digitalização 3D havia reduzido os lançamentos dos produtos para apenas um ou dois meses, em média, após os conceitos iniciais do projeto.
O projeto Jeep JK também destacou outra vantagem da digitalização 3D: a aquisição dos locais de montagem. Para facilitar a instalação, a Bushwacker sempre tenta usar apenas pontos de montagem da fábrica para seus acessórios. Para o alargador de para-lamas do estilo pocket, isso levou a uma combinação inovadora de alargamentos internos e externos, e os dados digitalizados forneceram as localizações exatas dos pontos de montagem em relação aos painéis do chassi.
"Sem a digitalização a laser, talvez não fosse possível lançarmos os acessórios para o Jeep JK."
Sterling Logan, engenheiro de projetos, Bushwacker
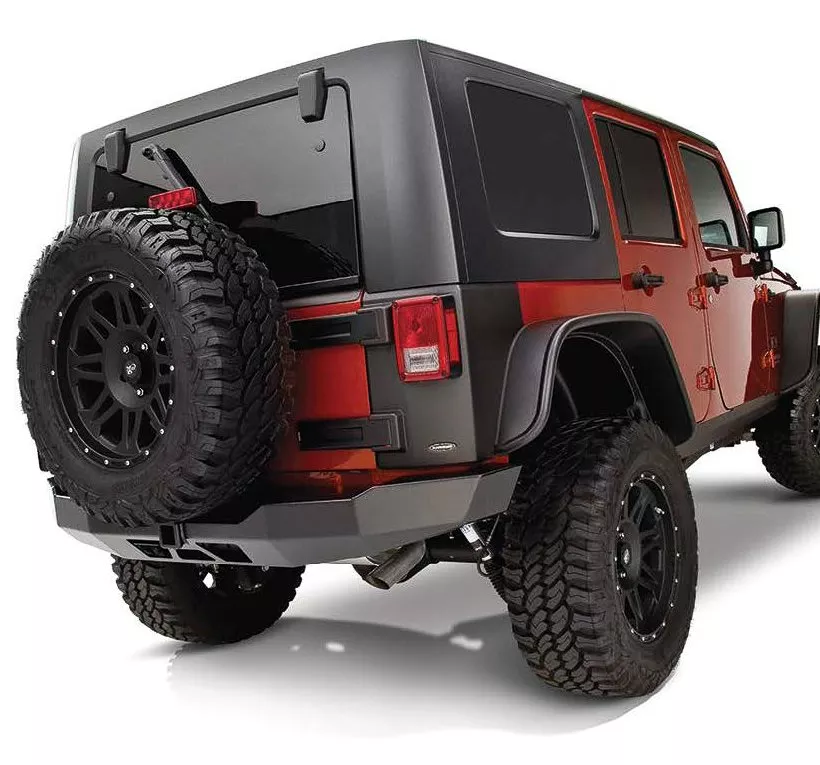
O design inovador e a atenção aos detalhes forma recompensadores na criação dos acessórios do Jeep JK. Na SEMA, os alargadores de para-lamas planos da Bushwacker conquistaram o segundo lugar na categoria Melhor Novo Produto na categoria Off-Road/Tração Quatro Rodas, enquanto seu Trail Armor conquistou o primeiro lugar como Melhor Novo Produto na categoria Acessórios Externos.
Os benefícios
Digitalização 3D na Bushwacker
Para todos os projetos, a Bushwacker combina seu braço de digitalização a laser, o PolyWorks e o Siemens NX (anteriormente chamado Unigraphics NX) em um processo com três etapas: digitalização, preparação e design.
Em alguns casos, o sistema de digitalização 3D desloca-se até o veículo alvo, mas na maioria dos casos, a Bushwacker leva o veículo para suas instalações. Para a primeira etapa do processo, a Bushwacker usa o PolyWorks|Modeler™ para controlar o scanner a laser e capturar os dados ao vivo. “Com o PolyWorks, não existe aquele processo exaustivo de configuração para que tudo esteja se comunicando antes de iniciarmos a digitalização” e, de acordo com Logan, leva apenas 10 a 15 minutos para configurar e iniciar a digitalização. Ele acrescenta: “Alem disso, a interface é intuitiva e fácil de usar.”
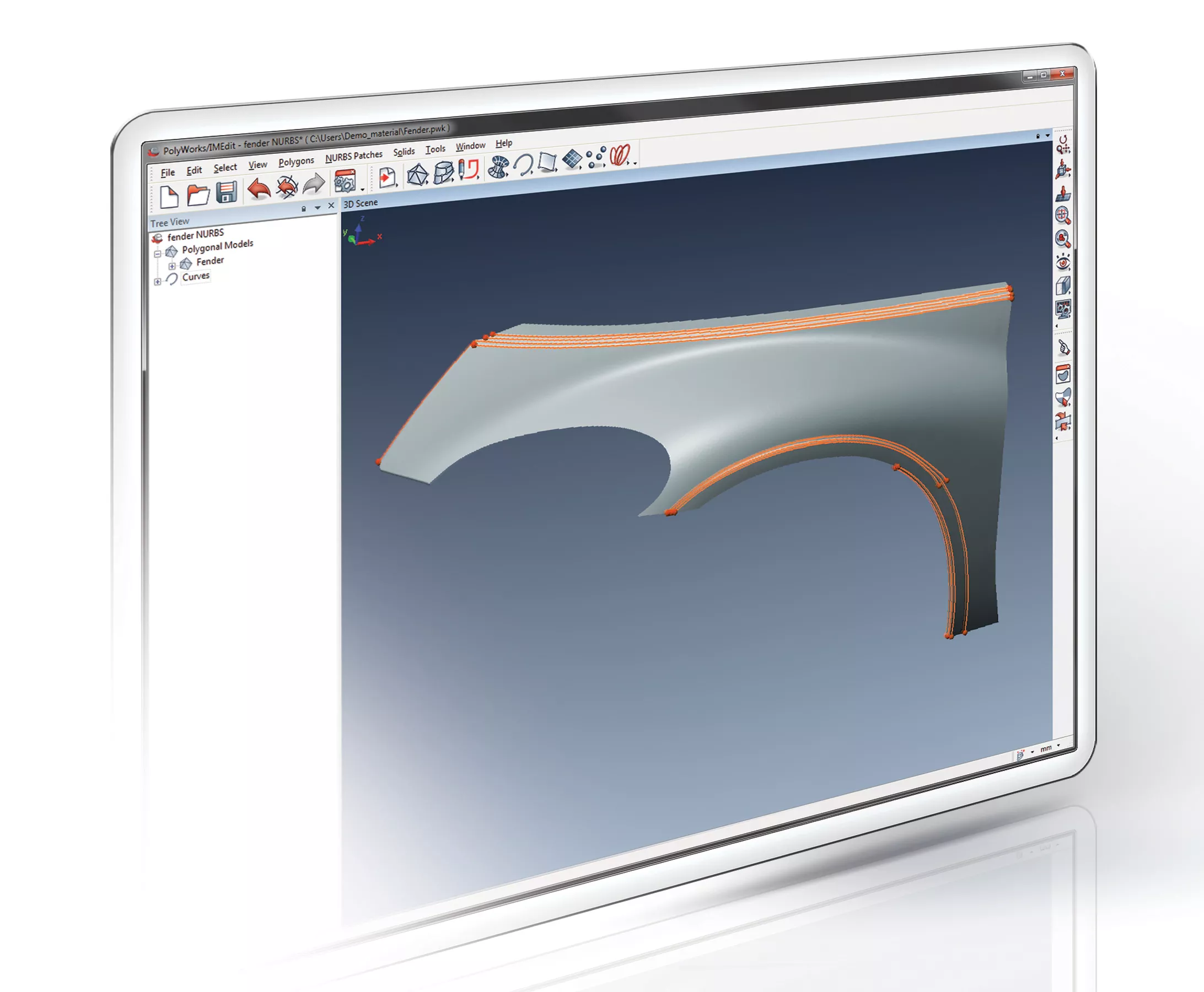
No PolyWorks|Modeler, é fácil extrair as entidades geométricas com as linhas mais finas.
O modelo digital muda dinamicamente para seguir o percurso da digitalização; ele fornece um ótimo feedback visual para permitir que o usuário saiba o que ainda precisa ser capturado!
“Adoro ver que, enquanto estou digitalizando, o modelo digital muda dinamicamente para seguir meu percurso de digitalização. Isso me dá um excelente feedback visual para me dizer onde estou e o que ainda preciso capturar”, reiterou Logan. Quando ele acha que a digitalização está terminada, ele passa para a ferramenta de comparação do PolyWorks, que mostra os desvios de digitalização para digitalização. “Esta é minha rede de segurança para um ocasional erro do operador, como uma colisão do scanner. Recebo feedback imediato sobre o que preciso digitalizar novamente”, disse Logan. “O resultado é dados limpos e precisos”, acrescentou.
Como usuário do Siemens NX, Logan também acha que a interface e as ferramentas do PolyWorks|Modeler são familiares e bastante semelhantes. Ele usa o PolyWorks para preparar os arquivos para importação no Siemens NX, a ferramenta que ele usa para manipulação dos dados e para design. “Precisamos de ferramentas de modelagem poderosas para criar peças e designs que sigam as linhas de estilo sutis do veículo. O PolyWorks nos ajuda a capturar os detalhes, e esses dados são usados no Siemens NX para projetarmos nossas peças. Para nós, é uma combinação perfeita”, declarou Logan.
Para preparar os dados para o Siemens NX, ele usa o PolyWorks para filtrar os dados com ruído, preencher furos e criar splines e superfícies NURBS. “Eu seleciono uma área e deixo o PolyWorks criar automaticamente os splines; depois, os conecto e crio as NURBS”, disse Logan. “Acho que é muito semelhante ao processo do Siemens NX, portanto, é muito intuitivo. Pelo que eu saiba, nada é melhor - nada é mais fácil do que o PolyWorks”, disse Logan.
No Siemens NX, as NURBS geradas pelo PolyWorks tornam-se a linha de base para o design de acessórios. A partir dos painéis da carroceria e dos pontos de montagem, a visão da Bushwacker toma vida. Durante o processo, os projetistas renderizam o acessório e o veículo para visualizar a forma e o ajuste.
Cada peça nova passa por uma revisão de design "digital" antes que os moldes do protótipo sejam projetados e usinados em uma CNC. “Os dados de superfície de alta qualidade que o PolyWorks fornece nos permitem examinar a peça no CAD para verificar o ajuste e acabamento antes mesmo de fazermos uma peça real”, observou Logan. Mesmo assim, eles ainda contam com protótipos físicos para fazer uma avaliação final. Logan diz: "As coisas se realçam quando você monta um alargador de para-lamas no veículo pela primeira vez; coisas que você não pode ver ou que não dá para ver na tela.”

Do modelo digitalizado a superfícies NURBS suavizadas no PolyWorks|Modeler.
O próximo passo
Recentemente, a Bushwacker aumentou sua confiança no PolyWorks e passou a usá-lo para inspeções. O PolyWorks|Inspector™ confirma a alta qualidade - marca de reconhecimento característica da empresa - de seus moldes, protótipos e primeiras amostras de produção. “O PolyWorks|Inspector é extremamente poderoso. Ele nos permite fazer a inspeção internamente, e isso nos permite avaliar peças e moldes de forma rápida e sempre que necessário”, afirma Logan. Ele conclui: “Na economia atual, temos que permanecer na vanguarda e o PolyWorks nos ajudou a fazer isso".