Pasión por el diseño y la perfección
Bushwacker Inc. recurre a las capacidades de ingeniería inversa de PolyWorks|Modeler™ para pasar del concepto al prototipo en solo unos días.
Durante casi 40 años, Bushwacker Inc., una empresa familiar en Portland, Oregon, ha fabricado molduras para guardabarros y accesorios para camiones para el mercado de refacciones para automóviles con pasión y orgullo. Reconocido como un fabricante líder, Bushwacker crea diseños innovadores y produce artículos de alta calidad. Como dijo Sterling Logan, Ingeniero de Diseño de Bushwacker, “Para hacer esto, necesitamos herramientas de vanguardia”.
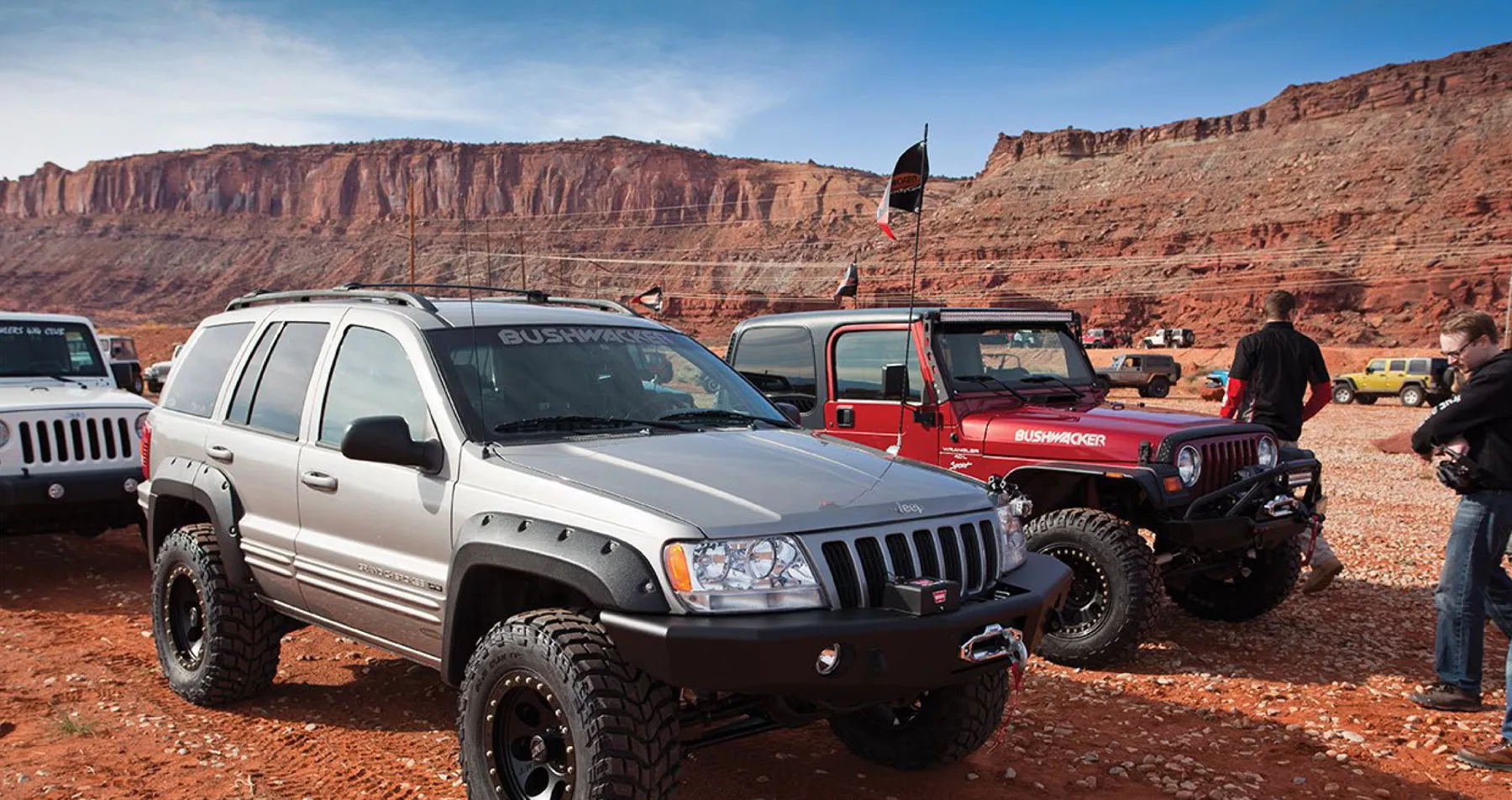
El desafío
Bushwacker está comprometido con el estilo y la innovación es parte de cada producto que fabrica. Cada detalle de cada diseño se examina meticulosamente, utilizando los últimos estándares en diseño y fabricación. Para Bushwacker, la calidad se puede resumir en tres palabras: ajuste, acabado y estilo. Sin embargo, Logan señaló que “la calidad es un objetivo en movimiento”. Los fabricantes de equipo original (OEM) siguen poniendo estándares cada vez más altos para la calidad de los vehículos en términos de ajuste y acabado, mientras las líneas del estilo de la carrocería se vuelven cada vez más sofisticadas. Y para seguir siendo competitivos, los productos de Bushwacker deben hacer lo mismo.
Garantizar la calidad para seguir siendo competitivos
“Nuestros clientes esperan que los accesorios se combinen con las líneas de estilo del vehículo. Y con las superficies de alta calidad que producen los fabricantes de automóviles, la menor interferencia con las líneas de estilo del vehículo o el más mínimo espacio se hace obvio de inmediato. Así que tenemos que entregar un producto que se ajuste perfectamente ”, dijo Logan. Para alcanzar este objetivo, el escaneo 3D es fundamental.
Después de experimentar con soluciones alternativas y servicios de escaneo, Bushwacker adquirió un sistema de escaneo de gama alta que incluye un brazo Romer Infinite 2.0 de siete ejes, un escáner láser Perceptron ScanWorks V5 y el software de metrología 3D PolyWorks® de InnovMetric. Conocer los datos digitales precisos de las superficies de un vehículo le permite a Bushwacker enfocar su talento en el diseño de los productos con la confianza de que se ajustarán perfectamente. Con el escaneo 3D, el ajuste se elimina de la ecuación mientras se simplifica el proceso y se reducen las horas de trabajo.
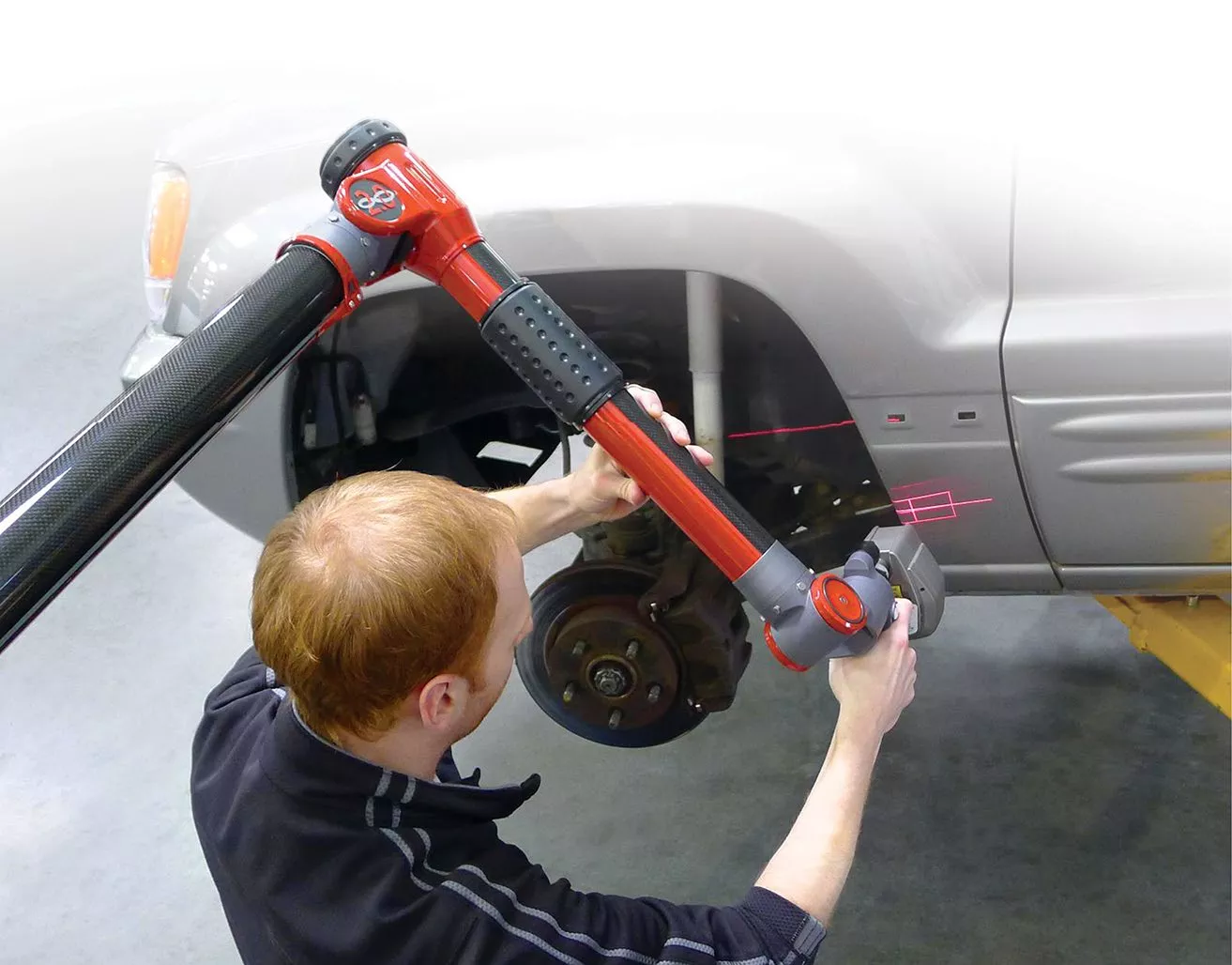
Escaneo láser de un Jeep Grand Cherokee para capturar el panel del cuarto frontal con sus líneas de estilo y ubicaciones de montaje.
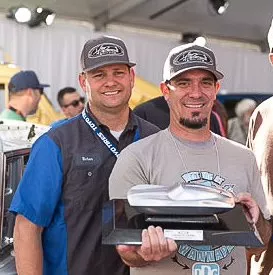
"Con el escáner y el software de PolyWorks, podemos pasar del concepto al prototipo en solo unos días."
Sterling Logan, Ingeniero de diseño de Bushwacker
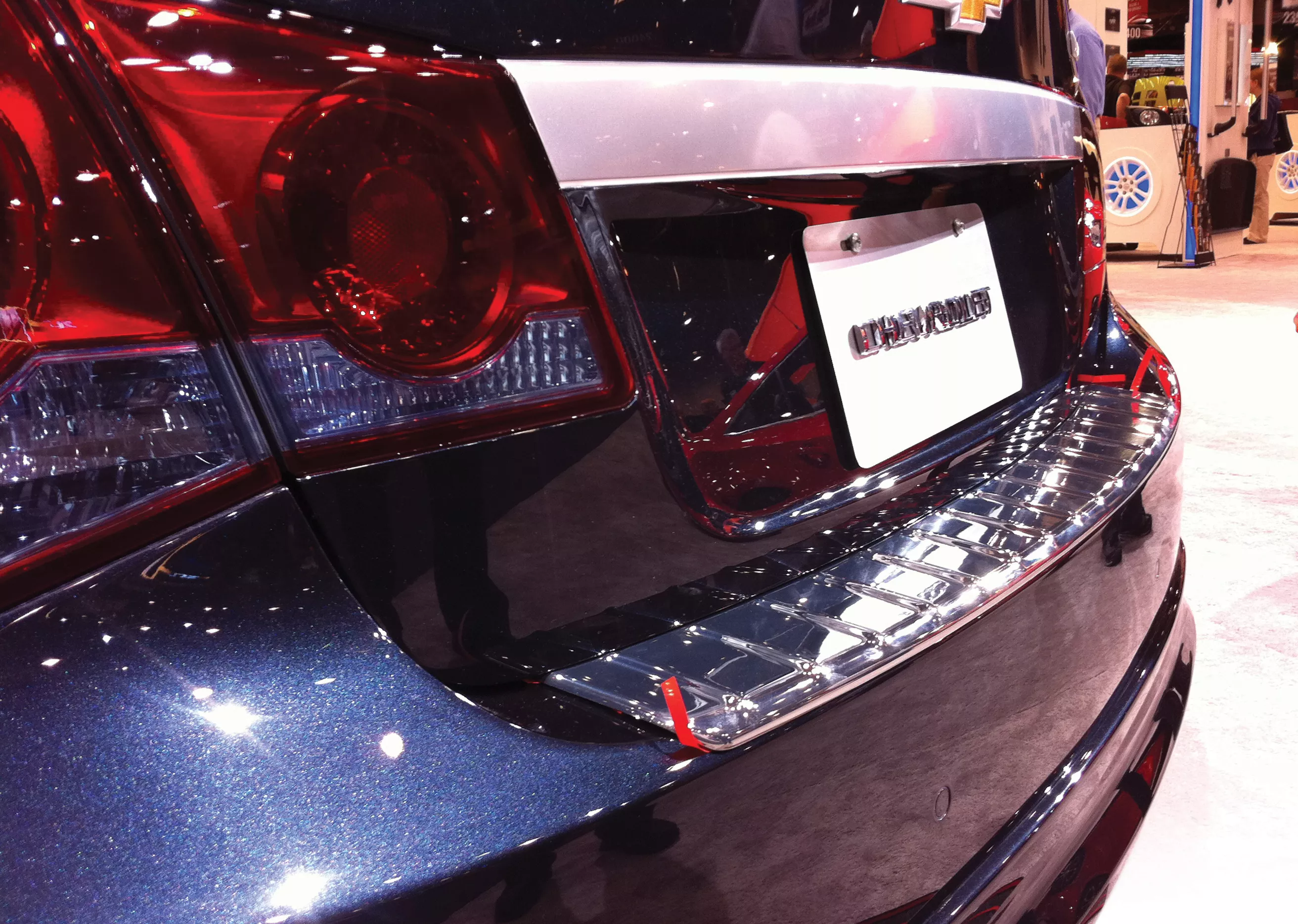
Protector de guardabarros en el Chevrolet Cruze en la SEMA, tres días desde el concepto hasta el diseño.
Para resaltar el rápido tiempo de respuesta gracias al escaneo 3D, Logan citó el siguiente ejemplo. “Un cliente se comunicó con nosotros unos días antes de la exposición de la Asociación del Mercado de Equipos Especializados (SEMA) con una solicitud personalizada para diseñar un protector de guardabarros para el Chevrolet Cruze. En tan solo tres días, teníamos prototipos de protectores de guardabarros y abrimos la exposición con un producto completamente nuevo.”
Logan ilustró cómo se completó el producto en solo tres días. El primer día, Bushwacker escaneó el Chevrolet Cruze, procesó los datos con PolyWorks|Modeler y los importó a Siemens NX. El segundo día, diseñaron el protector del guardabarros y mecanizaron un prototipo de molde. El tercer día, las piezas se fabricaron y se enviaron en avión a la exposición de la SEMA.
En sus primeros años, Bushwacker utilizaba el material preferido en los talleres donde se diseña el estilo de las carrocerías de los OEM: arcilla. Los diseñadores aplicaban arcilla al vehículo y lo esculpían minuciosamente con el diseño deseado. Luego, la forma resultante se transfería a plantillas de madera para que el estilo pudiera replicarse en arcilla en el lado opuesto del vehículo. A continuación, se fabricaban moldes de yeso a partir de los modelos de arcilla, y estos se utilizaban para fabricar prototipos de herramientas de termoformado.
Según Logan, este proceso consistía en muchas horas de trabajo minucioso. Y, aún en ese momento, les tomaba meses tener un molde listo para producción. Logan dijo: “Nos acercábamos, pero rara vez nos quedaba perfecto en el primer intento”. Obsesionado con la calidad de sus diseños, Bushwacker modificó el ajuste y el diseño mediante cuatro o cinco ciclos de moldes de prototipos, la verificación del ajuste, la evaluación visual, la modificación de los moldes y más revisiones.
“Pero ahora, con las capacidades de ingeniería inversa del escaneo láser y el software PolyWorks, rara vez tenemos que realizar cambios en nuestros moldes o diseños de piezas. Los cambios que hacemos están dedicados a las colas de diseño sutiles que dan su estilo a nuestras molduras, cada una diseñada para dar una apariencia específica ”, dijo Logan.
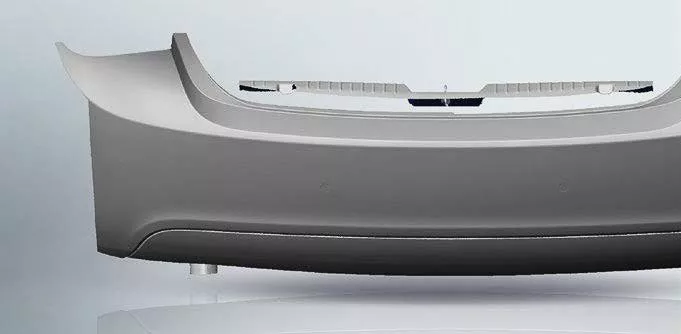
Los datos del escaneo del guardabarros trasero y el pestillo del maletero del Chevrolet Cruze están listos para usarse en el diseño del protector del guardabarros trasero.
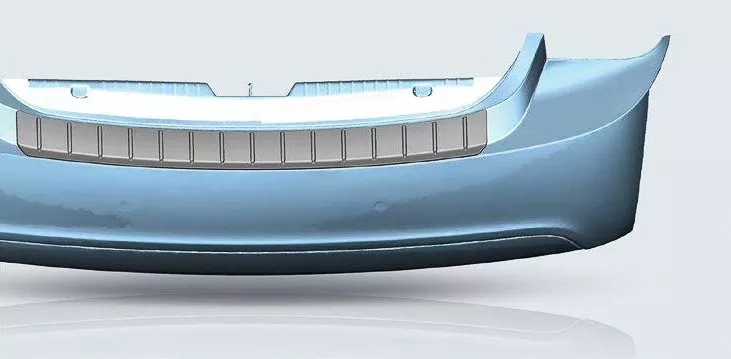
La imagen CAD muestra el diseño y la ubicación final del protector del guardabarros (gris) en el Chevrolet Cruz.
Jeep JK: pasión por el diseño
Logan reflexionó sobre el pasado y el presente: “Cuando comenzamos el negocio, nuestras primeras molduras fueron para el viejo Jeep CJ. El proceso de arcilla y yeso funcionaba bien porque la hoja de metal de los guardabarros era plana. Este definitivamente no es el caso del estilo de la carrocería del nuevo Jeep JK.”
El Jeep JK fue un desafío debido a sus líneas de estilo de carrocería y su configuración de montaje. Incluso con el escaneo 3D, Bushwacker pasó seis meses desarrollando sus molduras redondeadas patentadas, molduras de estilo plano y Trail Armor. Logan señaló que para todos los demás proyectos, el escaneo 3D, en promedio, ha reducido drásticamente el tiempo para lanzar los productos a solo uno o dos meses después de los conceptos iniciales.
El proyecto Jeep JK también destacó otra ventaja del escaneo 3D: la adquisición de las ubicaciones de montaje. Para facilitar la instalación, Bushwacker siempre intenta utilizar solo puntos de montaje de fábrica para sus accesorios. Para la moldura redondeada, esto condujo a una combinación innovadora de molduras internas y externas, y los datos escaneados proporcionaron las ubicaciones exactas de los puntos de montaje en relación con los paneles de la carrocería.
"Sin el escaneo láser, es posible que no hubiésemos podido lanzar los accesorios del Jeep JK".
Sterling Logan, Ingeniero de diseño de Bushwacker
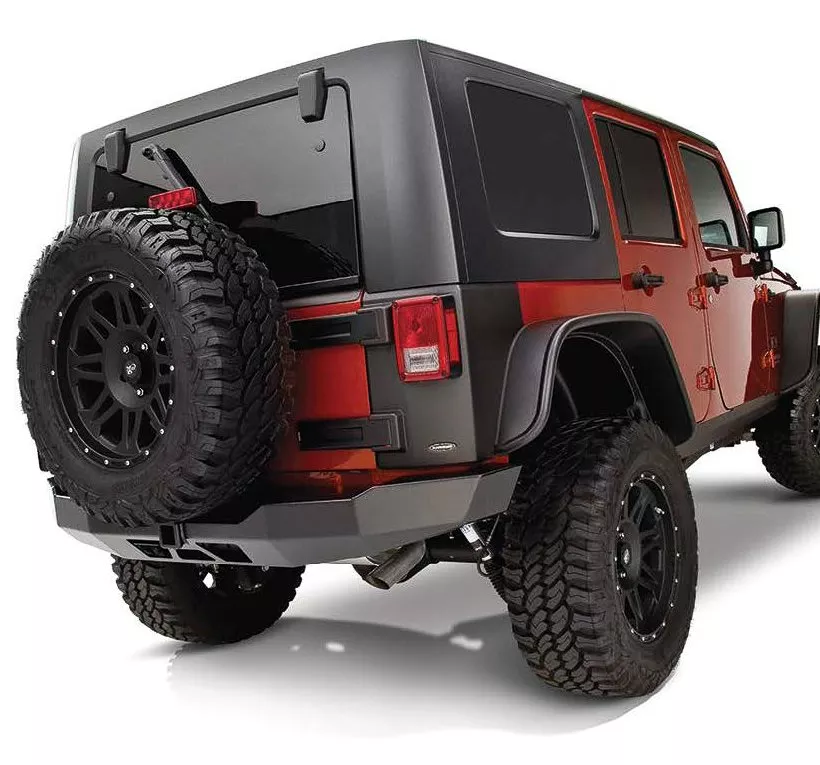
El diseño innovador y la atención al detalle valieron la pena para los accesorios del Jeep JK. En la SEMA, las molduras planas de Bushwacker obtuvieron el segundo lugar en la categoría de Mejor producto nuevo para vehículos todo terreno o con tracción en las cuatro ruedas, mientras que su Trail Armor obtuvo el primer lugar como el Mejor producto nuevo en la categoría de accesorios exteriores.
Los beneficios
Escaneo 3D en Bushwacker
Para todos los proyectos, Bushwacker combina su brazo de escaneo láser, PolyWorks y Siemens NX (anteriormente Unigraphics NX) en un proceso de tres pasos: escaneo, preparación y diseño.
En algunos casos, el sistema de escaneo 3D viaja al vehículo objetivo, pero en la mayoría de los casos, Bushwacker conduce el vehículo a sus instalaciones. Para el primer paso del proceso, Bushwacker utiliza PolyWorks|Modeler™ para el control del escáner láser y la captura de datos en vivo. “Con PolyWorks, no hay un proceso de configuración agotador para que todo se comunique antes de comenzar a escanear” y, según Logan, solo se necesitan de 10 a 15 minutos para configurar y comenzar a escanear. También comentó: “La interfaz también es intuitiva y fácil de usar”.
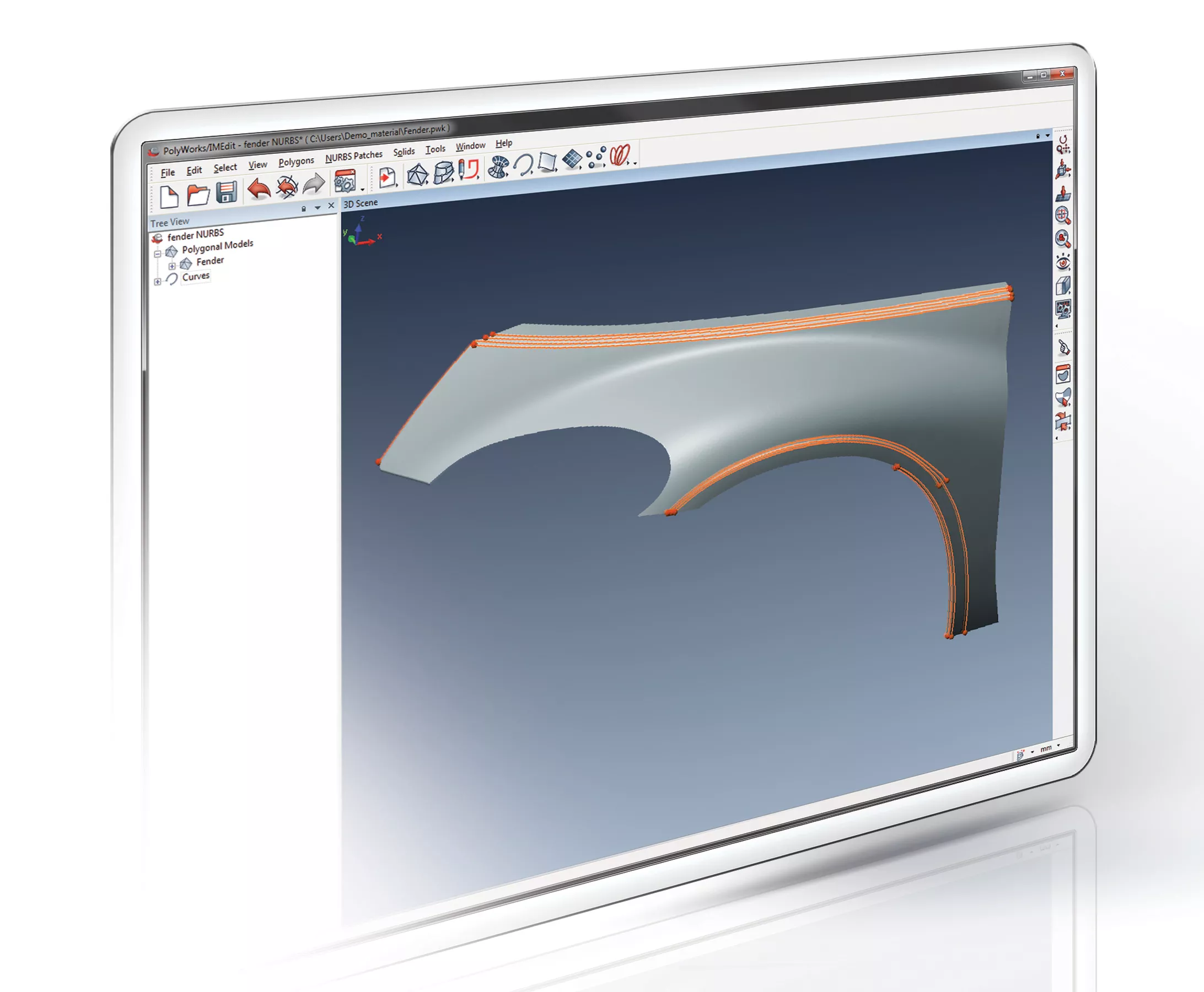
En PolyWorks|Modeler™, las líneas de las entidades geométricas más finas se extraen fácilmente.
El modelo digital cambia dinámicamente para seguir la trayectoria de escaneo; proporciona una excelente respuesta visual para que el usuario sepa lo que aún se necesita capturar.
“Me encanta que, mientras escaneo, el modelo digital cambia dinámicamente para seguir mi trayectoria de escaneo. Me brinda una excelente respuesta visual que me permite saber dónde estoy y lo que aún necesito capturar”, dijo Logan. Cuando considera que el escaneo está completo, recurre a la herramienta de comparación de PolyWorks, que muestra las desviaciones de un escaneo a otro. “Esta es mi red de seguridad para los errores ocasionales de los operadores, como cuando el escáner se golpea. Inmediatamente recibo información sobre lo que necesito volver a escanear”, dijo Logan. “El resultado son datos limpios y precisos”, agregó.
Como usuario de Siemens NX, Logan también considera que la interfaz y las herramientas de PolyWorks|Modeler le son familiares y son bastante similares. Utiliza PolyWorks para preparar los archivos para importarlos a Siemens NX, que utiliza para la manipulación y el diseño de datos. “Necesitamos herramientas de modelado potentes para crear piezas y diseños que sigan las sutiles líneas de estilo del vehículo. PolyWorks nos ayuda a capturar los detalles y esos datos se utilizan en Siemens NX para diseñar nuestras piezas. Para nosotros, es una combinación perfecta”, afirmó Logan.
Para preparar los datos para Siemens NX, usa PolyWorks para filtrar cualquier dato ruidoso, rellenar agujeros y crear splines y superficies NURBS. “Selecciono un área y dejo que PolyWorks cree automáticamente los splines; luego los conecto y creo NURBS ”, dijo Logan. “Me parece que es muy similar al proceso de Siemens NX, así que, de hecho, es intuitivo. Hasta donde sé, no hay nada mejor, nada es más fácil que PolyWorks ”, dijo Logan.
En Siemens NX, los NURBS generados por PolyWorks se convierten en el punto inicial para el diseño de accesorios. Desde los paneles de la carrocería y los puntos de montaje, la visión de Bushwacker toma forma. Durante todo el proceso, los diseñadores renderizan el accesorio y el vehículo para visualizar su forma y ajuste.
Cada pieza nueva pasa por una revisión de diseño ‘digital’ antes de diseñar y mecanizar por CNC cualquier molde de prototipo. “Los datos de superficie de alta calidad que proporciona PolyWorks nos permiten examinar la pieza en CAD para determinar el ajuste y el acabado antes de hacer una pieza real”, señaló Logan. Sin embargo, todavía se basan en prototipos físicos para la evaluación final. Logan dijo: “Las cosas te saltan cuando montas una moldura en el vehículo por primera vez, cosas que no se ven o que no ves en la pantalla.”

Desde el modelo digitalizado hasta las superficies NURBS lisas en PolyWorks|Modeler™.
El siguiente paso
Recientemente, Bushwacker extendió su uso de PolyWorks a la inspección. PolyWorks|Inspector™ confirma la alta calidad de los moldes, prototipos y primeras muestras de producción, por la cual la empresa es reconocida. “PolyWorks|Inspector es extremadamente poderoso. Nos permite llevar la inspección internamente, lo que nos permite evaluar piezas y moldes rápidamente y cuando sea necesario ”, dijo Logan. Concluyó: “En la economía actual, tenemos que mantenernos a la vanguardia y PolyWorks nos ha ayudado a lograrlo.”